高原材料利用率,降低核心零部件制造成本。不同原材料价格差异较大。某些应用领域的原材料价格昂贵。比如钛合金,传统钛基材料达到了9.8万元/吨,价格已是高昂;而根据Wohlers,2021年3D打印的钛基材料达到了36.3万元/吨,同比增长200%以上。3D打印逐层堆叠的特点可以减少原材料的浪费,较大程度提升了原料利用率,从而降低核心零部件的制造成本。
增材制造可以缩短“设计-验证-生产”全流程周期,提高产品制造效率。传统制造模式中产品设计验证需要经历大量的定型前产品试制,不断对产品进行改进,最终实现定型。增材制造技术能够使用建模软件进行产品的优化设计,并且可以实现产品的快速制造,以钛排气装置为例,根据3D Systems,增材制造可以实现装置的整合式设计与制作,产品设计时间从6周缩短到6天,零部件数量从20个降低到1个,此外生产时间也仅为之前的1/4,大大缩短了流程周期,提高制造效率。
02
市场现状
1、全球市场
全球3D打印行业蓬勃发展,预计2030年达850亿美元
根据Wohlers数据,2021年全球增材制造产值(包括产品和服务)152.44亿美元,同比+19.50%,其中增材制造相关产品(包括增材制造设备销售及升级、增材制造原材料、专用软件、激光器等)产值为62.29亿美元,同比+17.50%,其中设备销售收入31.74亿美元;增材制造相关服务(包括增材制造零部件打印、增材制造设备维护、技术服务及人员培训、增材制造相关咨询服务等)产值为90.15亿美元,同比+20.90%。
根据相关预测,2025年全球增材制造收入规模将达到298亿美元,2021-2025年CAGR为18.24%;2030年增材制造收入规模将达到853亿美元,2025-2030年CAGR为23.41%。
(1)国内行业进入稳增长赛道,预计26年市场规模超千亿元
2022年国内3D打印市场规模达320亿元,设备与打印服务为主要细分领域。当前国内3D打印行业政策分为支持类和规范类,鼓励企业进入行业的同时也抬高了行业标准,2017-2022年市场规模稳步爬坡上扬,期间CAGR为26.7%;亿渡数据预计26年国内3D打印行业市场规模将达1101.9亿元,22-26年CAGR为36.22%,仍将保持高速增长趋势。
行业规模全球占比17%,仍处成长上升期:2021年全球增材制造市场规模达到152.44亿美元,中国占比约为17%;当前全球3D打印头部企业主要集中在美国,我国3D打印行业仍处于成长早期,多项专利通过申请但未投入具体应用,核心技术与尖端人才是制约我国当前3D打印产业发展的关键因素。
(2)国内正处发展上升期,竞争态势尚且相对温和
凭借我国相关政策驱动,以及政策指引下企业端、研发端、资本端等齐力发展,推动3D打印行业迎热潮大发展。2021年国内以增材制造为主营业务的上市公司已有22家,实力较为雄厚的有铂力特、先临三维、华曙高科等。
我国3D打印区域特点为:京津冀全国领先,长三角地区凭借良好的经济发展优势、区位条件基础,已初步形成全3D打印产业链发展形式;而华中部地区以研发为主,以陕西、湖北为核心建立产业培育重地;珠三角地区则为3D打印应用服务的高地,主要分布在广州、深圳等地。
(3)国内3D打印行业逐渐获得资本市场和风投机构青睐
当前国内3D打印行业的投融资项目主要集中在A、B轮次,多数企业处于成长早期、潜在空间较大。总体上看,资本市场与投资者认为3D打印行业具有较大潜力空间,近年来投融资总金额逐步增加,2021年国内3D打印行业投融资项目/投融资总金额达34个/48亿元,2022年国内3D打印行业投融资需求超70亿元。由2021年国内3D打印行业融资轮次资料显示,融资项目主要集中在A轮(12个)、B轮(10个),这意味着现阶段大部分企业仍处于成长早期,具有较大成长空间。
03
政策环境
1、全球视角:以美国为代表的发达国家,政策出台早,力度大
早在2012年,美国国防部、能源部、宇航局、商务部等政府部门与企业、学校、非营利组织共同出资成立了国家增材制造创新研究所。而欧盟早在上世纪80年代就开始为3D打印项目提供资金,并在2004年组建了欧洲3D打印技术平台。总体来看,增材制造在多国被列为国家级重大战略,政策扶持力度大。
(1)我国近年出台大批扶持政策,但力度有待进一步提升
2017年发改委发布《增强制造业核心竞争力三年行动计划(2018~2020年)》,提出“发展重大技术装备整机和成套设备,加强重大技术装备研发和产业化能力建设”。2021年,增材制造相关技术被列入《“十四五”智能制造发展规划》。但总体而言,增材制造领域尚无专门国家战略级政策文件,相比美国,政策支持力度有待进一步提高。
(2)我国金属增材制造标准化水平仍存不足,当前正加速推进
美国目前已建立从“General Top-level”、“Category”到“Specialized”三层标准体系,覆盖设计、测试、安全、数据传输等诸多领域,标准体系完备。而根据国标委等六部委发布的《增材制造标准领航行动计划(2020-2022年)》,我国增材制造仍存在标准缺失、国际标准跟踪转化滞后、市场主体参与国内国际标准化工作程度不高等问题。近年来,我国增材制造标准化工作快速推进,一批增材指标标准陆续推出。
04
产业限制与突破
1、限制因素
多种限制因素,阻碍增材产业化发展。虽然在发展历程中技术不断迭代,但增材制造的本质仍是对材料进行不同方式的熔融后逐层堆积形成产品,这个过程实际上对原材料、设备都提出了不同于传统制造的各种要求,包括:
增材制造方案整体成本较高,目前以低价格敏感度领域为主。增材制造作为新兴行业,市场化历程短暂,设备相对传统设备结构复杂,原材料、生产工艺等相对传统制造也要求更高,所以增材制造方案整体成本相对较高,下游客户也主要集中在各应用领域实力雄厚的头部厂商。故目前仍以低价格敏感度的航空航天、医疗等领域为主。
原材料种类有限,限制产品生产范围。为了保证原材料能够完成较好的熔融烧结并逐层堆积,3D打印使用的粉末有特殊性质要求,粉末的含氧量、流动性、粒度等都有不同要求,使得新材料的研发成本较高,原材料范围有限。整体来看,在产业化发展起步时期,增材制造的新型材料应用周期较长,限制了3D打印技术在部分细分领域/场景的应用。
打印尺寸受技术限制,微型/大型零件制造难度较高。通常3D打印最大一次性成型尺寸取决于打印机的打印空间大小,而最小尺寸则取决于可打印的最小壁厚。当前3D打印设备的尺寸通常处于毫米级到米级,尺寸局限相对传统制造较大。
2、产业突破
前期抑制因素有所改善,产业化有望加速。受制于上述因素,前期3D打印的可应用领域相对较窄,下游客户需求较低,通用化进程较慢。但随着技术持续突破和产业政策引导,前期因素得到改善,3D打印产业化有望加速。
(1)研发投入叠加下游需求催生规模化,产业链全环节持续降本
随着美欧的3D打印底层技术专利在2009-2015年陆续到期,我国增材制造产业在研发领域障碍消除,研发投入得以提升。叠加部分领域对零件制造的工艺精度、技术难度和全流程成本要求的提高,增材制造快速成型、提升生产效率的特点不断被发掘,增材制造产业化深入,中下游厂商开始向上拓展。GE、HP等下游应用公司纷纷布局3D打印产业,巴斯夫、杜邦等企业进入原材料领域,研发投入和市场规模效应显现使得产业链各环节降本显著。
(2)原材料持续丰富,助力设备端发展
随着增材制造产业化的推进,原材料和中下游的紧密联系,使得中游设备制造厂商和下游应用厂商均开始布局原材料领域。增材制造原料供应商逐年增长,2017年到2021年从98家增长到230家,4年CAGR29%。而随着供应商增加和研发投入增长,原材料种类也愈发丰富。2021年全球增材制造原材料种类超过2800种,四年CAGR达38%。
随着工业技术的不断进步和在增材制造技术产业化领域的不断投入,3D打印的设备性能不断提升,打印尺寸也在不断增大。SLM Solution于2022年推出3x1.2x1.2米的超大尺寸粉末床激光熔融金属3D打印机,可生产直径1.8m、高1.6m的圆柱形零件或是3m*1.2m*1.2m的长形零件。
1、产业链概况
3D打印行业大致可以分为上中下游三个环节。其中上游环节为原材料及零件,包括3D打印原材料、核心硬件和软件等,中游为3D打印设备和服务,其中在产业发展初期国产化率尚不高的情况下还存在3D打印设备代理商,下游主要为航空航天、汽车、医疗、消费及电子产品等领域。
通过梳理现有增材制造国内上市公司公告,绘制以下增材制造产业链图谱:增材制造定制化产品端,以铂力特为代表企业,通过向上游采购增材制造设备(或采购设备零部件自主研发制造打印设备)以及增材制造金属粉末,制造定制化产品销售给下游客户,其主要客户为中航工业集团、航天科工集团等军工央企集团;增材制造设备端,以铂力特、华曙高科为代表企业,其通过向上游采购光学器件、机械加工零件等组装打印设备,其中振镜、激光器等先进零件仍需进口。打印设备的主要客户仍为各大军工集团,其一方面直接采购增材制造零部件上机使用,另一方面也会采购打印设备,用于新型号的前端研发以及小批量试制;增材金属粉末方面,以有研粉材为例,其通过采购各类金属原材料雾化制粉,销售给铂力特、鑫精合以及各大军工集团。
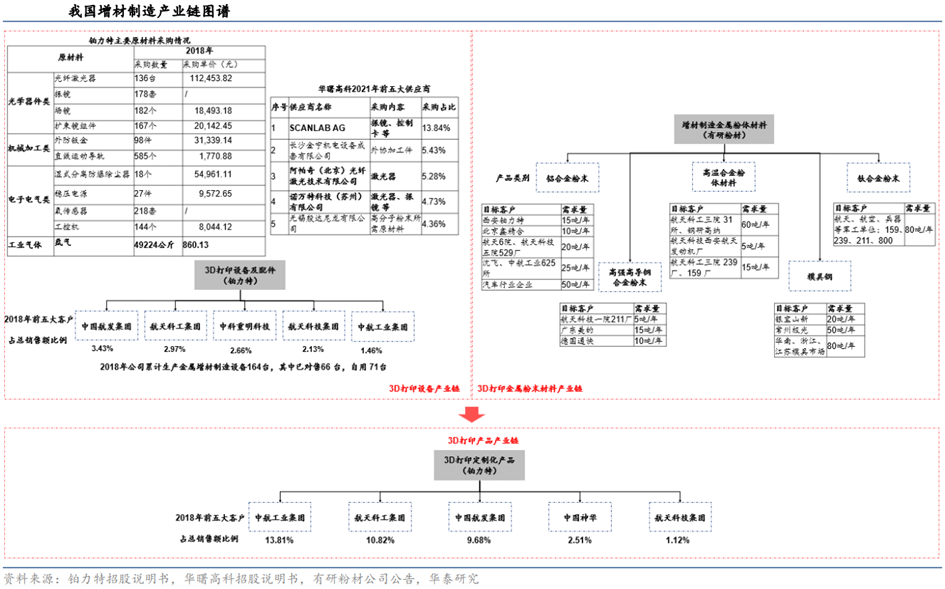
2、上游:增材制造行业上游主要包括3D打印原材料、核心硬件和软件服务
3D打印原材料:是影响产品质量的重要因素,目前使用的金属粉末要求纯净度高、球形度、粒径分布窄、氧含量低。当前国内的金属3D打印材料已经基本满足国产设备及下游需求,设备厂商一般与第三方材料厂商合作开发各类金属材料及熔融工艺,少量3D打印设备及打印服务厂商会自主生产金属3D打印材料。目前国内比较知名的3D打印粉末提供商包括有研粉材、中航迈特、威拉里、宁波众远、西安赛隆等。
核心硬件:增材制造使用的核心硬件包括振镜和激光器,目前国内大部分企业主要采购自美国和德国,存在依赖进口的情况(以华曙高科为例,2022年上半年振镜国产化率为0.9%,激光器国产化率为30.1%)。随着国产振镜和激光器的研制成功及性能提升,目前已实现部分进口替代。比较有名的激光器或振镜提供商包括锐科激光、创鑫激光、大族斯特、正时精控、金橙子等。
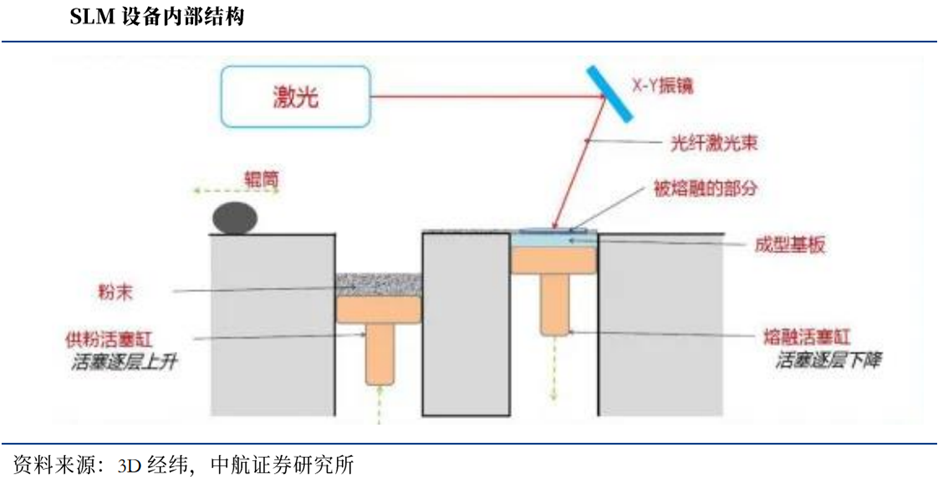
软件服务:3D打印软件包括工业软件及应用软件,应用软件主要是产业链上下游主体基于需求开发提供,如辅助设计、工程处理、仿真模拟、智能处理软件,工业软件系统指控制3D打印设备的控制系统,是3D打印设备的核心中枢。目前行业内的大部分设备的工业系统大部分向第三方采购,软件性能提升依赖于软件服务。国内比较有名的工业软件服务商为安世亚太。
3、中游:增材制造行业中游主要包括3D打印设备制造商和设备技术服务提供商
3D打印设备:其中3D打印设备是中游,也是产业链的核心主体。增材制造设备制造商研发、生产打印设备提供给下游客户使用,并根据客户反馈不断更新换代,向上游传递市场需求,推动产业链水平提升;
3D打印服务:近年来,随着增材制造需求的提升,出现了增材制造服务提供商,主要通过3D打印设备为客户提供打印服务及各类衍生的技术服务;
3D打印设备代理商:由于打印应用需求的增多以及打印设备厂商数量的提高,代理设备销售的中介企业也逐渐增多,随着上下游分散化趋势,代理设备企业将会进一步提高影响力。
4、下游:主要是各下游应用领域,包括航空航天、汽车、医疗、教育等领域
目前由于增材制造行业最有活力的领域是航空航天,因此主要的客户结构来自于科研单位及高校、各大巨头企业的研发部门以及军工单位的下属院所,此外增材制造在快速修复的领域的优势,使其在有相关需求的企业中有所应用,比如油气勘探中的钻头修复和更换,就使用了增材制造技术。
06
市场格局与行业壁垒
1、市场格局
3D 打印设备性能是 3D 打印企业的核心技术,其核心功能模块包括工业软件、控制系统,以及光学能量系统、机械及运动系统、风场系统等。全球金属3D打印设备主要参与企业包括华曙高科、EOS、SLM Solutions、铂力特,高分子3D印设备主要参与者包括华曙高科、EOS、HP、3D Systems。关于设备核心关注指标包括最大成形尺寸、振镜最大扫描速度、光学定焦技术、运控软件能力等。
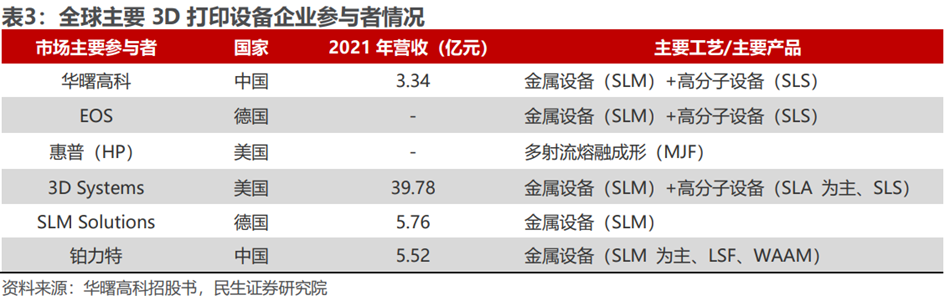
增材制造装备核心器件,如高光束质量激光器及光束整形系统、高品质电子枪及高速扫描系统、大功率激光扫描振镜、动态聚焦镜等精密光学器件、阵列式高精度喷嘴/喷头等严重依赖进口,激光器市场基本被Trumpf、IPG 等 3-4 家国外企业占有,扫描振镜市场则主要被德国Scanlab公司占有。
竞争门槛:增材制造是高科技、高附加值的技术密集型产业,技术壁垒高、设备资本投资大,同时在生产工艺、性能指标上较传统制造业有更高的技术要求。另外,产业定制化属性也使得公司需要深度参与客户产业的产业前期论证和定制化设计,具有较强的客户黏性。目前增材制造技术尚处于产业快速成长期,因此核心技术团队在经验上的积累十分重要,先发者具有人才和数据库优势;
技术壁垒:由于增材制造设备涉及到粉末的快速烧结和冷却,因此振镜的精确定位、风场对粉末溅射的抑制和晶格结构的形成等方面技术难度较高,目前仅有少数增材制造企业掌握性能达到锻造水平的飞机承力结构试验件的生产工艺,具有较高的技术壁垒;
认证资质壁垒:由于目前增材制造的零部件主要应用于航空航天高端领域,下游客户对于保密性和可靠性要求较高。此外,目前航空航天下游客户以飞机、导弹、卫星等零部件制造商为主,隶属于航空工业、航天科工、航天科技等企业,相关研发体系中的研发人员人脉背景较为封闭集中,因此具有较强的客户渠道壁垒。此外,由于航空航天产品每个型号均需要经过立项、试制、预研、试飞、列装等不同阶段,产品定型后,供应商更改的难度较大,因此深度参与型号预研的产品供应商在型号落地后,也会进入稳定的合格供应商名单。新进入者短期内无法进入,只能针对新型号进行试制和预研,因此具有很高的进入壁垒;
人才壁垒:由于增材制造行业目前处于快速发展期,因此不同的技术路线尚未成熟,需要大量的研发人员投入研发和试错,有经验的增材制造工程师可以针对需求设计零部件结构和支撑,由于增材制造技术的前部设计需要结合专业知识,在零部件加工时深度介入,而核心人才团队可以有效的针对需求设计响应的结构,从而完成业务,因此核心骨干团队非常重要;
先入壁垒:增材制造产业属于know-how领域,设备的稳定性和控制的精度直接决定了成型零部件的成品率和性能,因此熟悉工艺、具有设备制造技术的先入者凭借多年来积累的数据库和实践经验在产业链中通过长年的设备迭代,在设备的稳定性和零部件的成型经验上积累了较多的数据,具有较强的先发优势。另一方面,由于增材制造粉末价格较高,而累计的品牌效应将使得客户在面对高价值量零部件的情况下,更倾向于选择具有成熟经验、品牌力强的供应商。
07
相关企业
1、铂力特
铂力特是国内最具产业化规模的金属增材制造企业之一:公司专注于工业级金属增材制造(3D打印),为客户提供金属增材制造技术全套解决方案,业务涵盖:金属3D打印定制化产品服务、设备研发及生产、原材料研发与生产、结构优化设计开发和工艺技术服务(含定制化工程软件的开发等)。
金属3D打印定制化服务:公司主要使用三项技术:选择性激光熔化成形技术(SLM)、激光熔覆沉积技术(LSF)、电弧增材制造技术(WAAM),深耕航空航天领域,增材制造的零件广泛应用于弹箭星船机,可实现年交付零件50000余件。
金属3D打印设备研发及生产:公司自主研发了激光选区熔化成形、激光立体成形、电弧增材制造等系列金属3D打印设备。
金属3D打印原材料:公司在金属材料、功能材料、金属基复合材料等方面具有丰富的研究基础,在金属增材制造的新材料开发领域处于国际领先地位。
铂力特深耕航空航天领域,持续开发新产品、新市场,经营业绩稳定增长。2016-2022年公司营收自1.66亿增至9.18亿,CAGR为32.9%;归母净利润自3132.7万增至7949.9万,CAGR为16.8%。2022年,公司营收9.18亿(+66.3%),归母净利润7949.9万(+149%),2023Q1公司营收1.33亿,同比增长48.1%。
剔除股份支付影响,公司归母净利润逐年稳步提升:为了建立、健全公司的畅销激励机制,吸引和留住优秀人才,充分调动核心团队积极性,有效地将股东利益、公司利益和核心团队个人利益相结合,公司于2020年10月推出限制性股票激励计划。2016-2022年,公司剔除股份支付影响的归母净利润自3133万元增至2.42亿元,CAGR为40.6%。
盈利能力逐年提升:2016-2022年公司综合毛利率自42.9%提至54.6%(+11.7pct);剔除股份支付影响的归母净利率自18.8%提至26.4%(+7.6pct)。
3D打印定制化产品和3D打印设备及配件已成为公司两大核心主业,2022年营收占比合计96.5%。其中,2016-2022年3D打印定制产品营收占比自38.9%提高至50.9%,提升了12pct,始终是公司第一大业务。3D打印设备及配件营收占比自26.2%提升至45.5%(+19.3pct)。原材料营收占比由2.5%提至3.5%(+1pct)。随着公司自研3D打印设备的不断成熟,代理销售的营收占比逐年下降:公司主要通过子公司铂力特(香港)代理销售德国EOS公司的设备,2016-2022年该业务营收占比自29%降为0。
公司聚焦金属增材制造技术,持续加大研究开发和技术创新力度,提升公司竞争力。公司研发费率逐步提升:2016-2022年公司研发费率自9.1%提至17.7%(+8.6pct),2023Q1公司研发费率为31%(+0.4pct)。2022年公司进一步加强研发能力建设:研发费用1.63亿(+42.33%),研发费率17.7%,较2021年下降3pct,主要系营收增长幅度较大,研发费率有所降低。
金属&高分子两轮驱动,销售规模位于全球前列。华曙高科十余年来专注于工业级增材设备领域,致力于向全球客户提供一流的SLM(金属)和SLS(高分子)增材设备,并提供3D打印材料、工艺和服务。公司已开发20余款设备,并配套40余款专用材料及工艺,全面应用于航空航天、汽车、医疗、模具等领域。公司销售规模位居全球前列,是我国工业级增材制造设备龙头企业之一,下游客户包括航空航天科研院所、一汽大众、上海集团、潍柴动力等头部企业和高校,并和巴斯夫、宝马、捷普等建立战略合作关系。
2022年前三季度公司营收/利润增速达48%/73%,业务成长性明确。公司在2019-2021年营收/归母利润CAGR为47%/154%的基础上,2022年前三季度实现营收/归母利润2.75/0.55亿元,同比增长48%/73%,成长性较为明确。业务高增系前期航空航天预研装备部分批产,实现快速放量。展望未来,预计公司将受益“十四五”期间我国航空航天领域的强投入,叠加医疗、汽车、模具等业务在海内外顺利拓展,业绩有望保持高增态势。
拟募资6.6亿元用于研发投入和产能扩建,维持市场竞争力和业务发展动能。随着公司业务快速发展,2021年设备/原材料产能利用率已达113%/130%,用户侧装机量超700台,原有产线较难满足下游客户需求,车间和库房也逐渐饱和。根据华曙高科招股书,公司拟募资6.6亿元用于研发中心建设和产能扩张,两年内即可试投产,维持市场竞争力和业务发展动能,以享受产业化由0-1过程中的行业高增红利。
超卓航科是国内少数掌握冷喷涂固态增材制造技术并产业化应用在航空器维修再制造领域的企业之一,主要从事定制化增材制造和机载设备维修业务。
公司设立初期专注于航空机载设备维修:主要从事军用及民用航空器气动附件、液压附件、燃油附件和电气附件的维修业务。
公司建立了冷喷涂固态增材制造技术体系:经过多年研发创新,公司实现了多种金属材料的高强度沉积,并将冷喷涂固态增材技术成功应用于机体结构再制造领域;公司不断开发和拓展增材制造技术的应用场景和下游市场:研发出了适用于电子器件领域的靶材和适用于航空高温、高压环境的航空紧固件产品。
公司主要服务于军方及其下属飞机大修厂、军工集团下属单位以及民用航空运营企业等客户。基于公司在冷喷涂固态增材制造领域领先的技术水平、稳定可靠的产品质量及与军方的长期合作历史,公司是A、B基地级大修厂多种型号战斗机起落架大梁疲劳裂纹冷喷涂修复的重要供应商。
公司以定制化增材制造为核心主业,营收占比接近70%。2018-2021年,公司定制化增材制造业务营收占比自30.4%提至71.4%(+41pct),2022年该比例为67.9%,基本维持稳定。
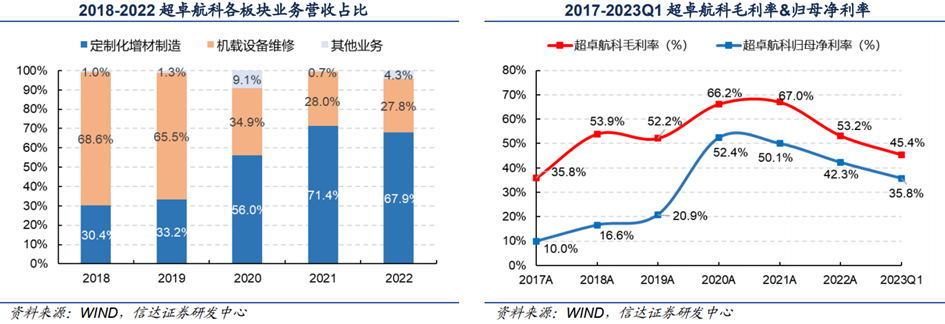
有研粉末新材料有限公司主要从事有色金属粉体的设计、研发、生产和销售,企业成立于2004年,自2012年起先后成立有研重冶、有研香港、粉末研究院等全资子公司,2018年进行股份制改革变更为有研新材料股份有限公司,2021年企业成功在上交所科创板上市。企业铜基金属粉体材料市场占有率居全国首位,于2021年获批工信部第六批制造业单项冠军产品,属国内金属粉体材料和袭击焊粉材料领域的龙头企业。
公司专注于有色金属粉体的研发制备,主要产品包括微电子锡基焊粉材料,铜基金属粉体材料和增材制造粉体材料,其中铜基金属粉体材料又包含电解铜金属粉体材料、雾化铜金属粉体材料与其他铜基金属粉体材料,产品核心性能指标对标欧美发达市场,市场占有率居全国榜首。有色金属粉体在多个行业均有广泛运用,如粉末冶金零部件多应用于汽车工业,超硬工具多应用于建筑、交通及国防工业等领域。
公司股权集中度较高,由有研科技集团控股,有研科技集团隶属国务院国资委,截至2022.12.31,有研科技集团持有36.31%的股份。恒瑞盛创、恒瑞合创、微纳互联为员工持股平台,于2019年6月成为股东,共持有公司5.15%的股份,公司其他股东持股比例较低且较为分散。公司下设康普锡威、有研香港、有研重冶、粉末研究院、有研合肥5家全资子公司,通过有研香港间接持有英国Makin与有研泰国全部股份,通过康普锡威间接持有山东康普全部股份。
营业收入稳步增长,盈利能力不断提升。收入端,公司营业收入由2018年的17.98亿元增长至2021年的27.81亿元,2019-2021公司营收CAGR为15.65%。2022Q1-Q3公司营收达21.3亿元,同比增长7.79%。利润端,由于近年金属原材料价格上涨,公司毛利水平呈下降走势,但由于增材制造用粉材料毛利较高,公司总体盈利能力较为稳定,营收与归母净利润呈上升趋势。公司2021年实现归母净利润0.81亿元,同比降低38.54%,主要由于2020年归母净利润包含非经常性损益搬迁收益7154.97万元,扣除这一非经常性损益,归母净利润同比增长34%。公司2022Q1-Q3实现归母净利润0.38亿元,受宏观经济以及南方地区高温限电等影响,同比降低22.03%。
先临三维科技股份有限公司主营业务是基于计算机视觉的高精度3D数字化软硬件技术的科技创新企业,研发、生产、销售齿科数字化和专业3D扫描设备及软件。主要产品和服务为扫描仪、打印机、耗材及配套设备、服务销售。
公司的发展历程可分为初创期、开拓期、扩张期和聚焦期四个阶段,经历了扩张的失控与重新聚焦的过程。自创立起,公司进行了多年增材制造产业化探索,进行了快速的扩张,拖累了公司的业绩。2018年至今,公司进行业务调整,剥离亏损的增材制造服务业务,重新聚焦齿科数字化和专业3D扫描,甩掉包袱,重回成长。
发展初期公司形成“1+4”业务发展布局。“1+4”业务布局即先临三维母公司为主体,加上易加三维、天远三维、云打印、捷诺飞四个专业子公司为主的业务发展布局。其中易加三维专注于工业金属增材制造;天远三维专注三维机器视觉检测技术;云打印公司构建覆盖全国的线上线下“增材制造+互联网”的分布式3D制造服务模式;捷诺飞生物专注生物材料和细胞增材制造技术研发。2021年公司剥离北京易加三维,使其单独融资发展,公司通过战略调整,聚焦齿科数字化与专业3D扫描业务。
2022年前三季度实现营业收入5.48亿元,同比增长38.73%;归母净利润亏损0.03亿元。2021年主营产品包括3D扫描仪、耗材及配套设备、3D打印机,占比分别为77.98%、10.99%、7.87%。
安徽楚江科技新材料股份有限公司的主营业务为铜基材料、钢基材料、新材料、高端热工装备的研制、生产和销售,楚江新材主要产品包括精密铜带、铜导体材料、铜合金线材、精密特钢、碳纤维复合材料和高端热工装备。楚江新材研制开发了新一代等离子旋转雾化制粉系统,解决了金属基3D打印粉体材料的产业化装备及技术难题。
2022年前三季度实现营业收入298.2亿元,同比增长9.73%;实现归母净利润1亿元,同比下降75.49%。2021年主营产品包括铜基材料,钢基材料,高端装备、碳纤维复合材料,占比分别为94.97%、2.56%、2.47%。
08
前景展望
1、我国增材制造产业正在迈向规模化、自主化、集聚化发展新阶段
根据工信部装备工业发展中心总工程师左世全在增材制造产业发展(广州)暨2023年增材制造产业年会上的报告《增材制造十年发展及展望》,我国增材制造产业发展呈现以下趋势:
(1)我国增材制造产业整体实现从研发创新向产业规模化发展蜕变
2012-2022年,我国增材制造产业规模自10亿元增至320亿元,CAGR为41.42%。预计2023年我国增材制造产业规模有望超过400亿元。按照25%的复合增长率保守估算,我国增材制造产业规模有望在2027年左右突破千亿元。
企业数量持续增加:我国增材制造全产业链相关企业数量超过1000余家,以增材制造为主营业务的上市公司数量从2012年的1家增长至2022年的22家(含新三板),规模以上企业数量由2016年的20余家增至2022年的近200家,其中规模过亿的企业数量由2012年的3家增至2022年的42家。
装备营收占比超过一半:2022年我国增材制造专用材料、零部件、装备、服务等各个环节营收占比分别约为12.4%、5.9%、53.2%和26%。
(2)我国增材制造装备实现从进口为主到自主生产转变
我国高精度桌面级光固化增材制造装备、多材料熔融沉积增材制造装备持续保持领跑并畅销海外;米级多激光器激光选区熔化装备、多电子枪电子束熔化装备、大幅面砂型增材制造装备等自主开发装备相关核心指标达到国际先进水平;超高速激光熔覆头、电子枪等十多类关键部件取得攻关突破和自主生产,其稳定性、可靠性得到不断改善。
我国增材制造装备海外认可度不断提高:2022年,我国增材制造装备(含消费级)出口228.7万台,较2019年增长59.7%,出口金额36.6亿元,较2019年增长近1倍。
(3)增材制造技术应用实现从原型制造向直接制造发展
由快速制造原型样件逐步向直接制造最终产品质变,已应用于航空航天、医药、汽车等国民经济39个行业大类、89个中类,覆盖产品结构设计、原型制造、批量生产、工装制作、保障修复等全寿命周期。
航空航天领域:新一代战机、国产大飞机、新型火箭发动机、火星探测器等重点装备的关键零部件逐步应用增材制造技术,解决了诸多过去难以制造的复杂结构零件成形问题,实现产品结构轻量化。
医疗领域:增材制造被应用于医疗植入定制、修复体制作、诊疗辅助器具制作、个性化矫正器具打印、细胞/组织/器官打印等;髋臼杯、脊柱椎间融合器等增材制造医疗植入物已获得NMPA认证,实现临床应用,拓展疾病治疗解决方案;增材制造技术实现口腔正畸牙模批量定制生产,解决传统机加工制造复杂的问题,满足患者个性化需求。
汽车领域:增材制造被应用于概念车、零部件创新、定制化夹具制造、内饰创新等研发试制方面,达到缩短研发周期,以及减轻重量、减少材料损失、自由定制配件、轻松更换备件等目的。
铸造领域:将增材制造技术应用于砂型铸造、熔模铸造等铸造工艺中,大大减少铸造加工流程,提升产品制造效率,实现对传统铸造的替代。
其他领域:增材制造被应用于建筑设施整体制造、文物复刻展示、高级手办、轻量化鞋品制造等。
从零散状、碎片化到成链条、集群化发展演变。2013年,全国首个3D打印产业园在陕西渭南建成,随后,广州3D打印技术产业园、安徽春谷3D打印智能装备产业园等20余个增材制造全产业链及相关配套服务的产业聚集地、产业园区在各地陆续涌现,初步形成珠三角地区、长三角地区为核心,京津冀地区和陕西、安徽等中、西部地区为纽带的产业空间发展布局。
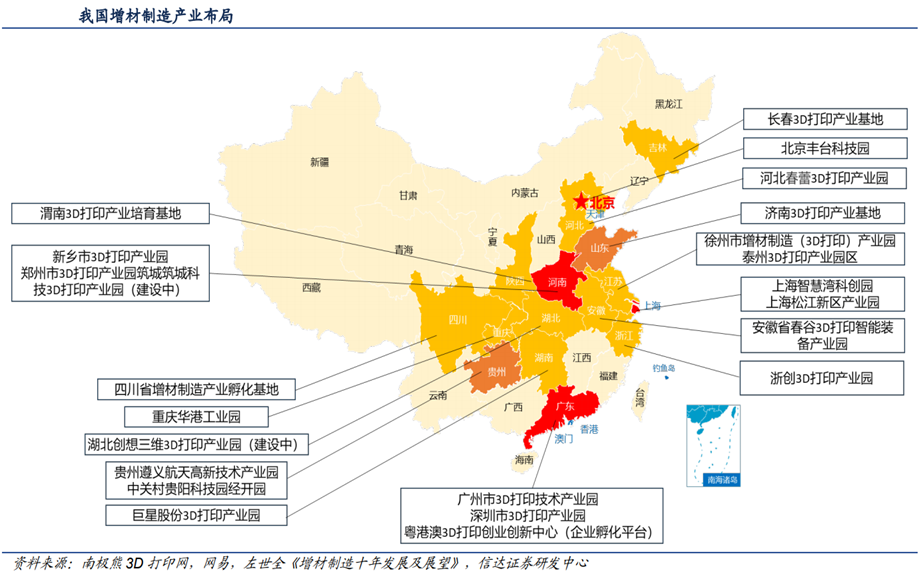
市场集中度有所下滑,国内主要增材制造设备企业尚在起步阶段。根据Wohlers Associates统计数据,2021年全球共计266家工业级增材制造设备生产商,其中美国、德国、中国地区生产商数量分别为59、38、37个,合计占比过半。随着行业新进入者增多,市场集中度有所下滑,2021年,全球增材制造龙头企业Stratasys市占率为12.0%,同比下滑1.5pct(2019年公司市占率16.6%,2020年公司市占率13.5%,呈现逐年下降趋势);而与此对应,2021年“其他”项生产商占比提升3.9pct至39.8%。从生产商销售数量来看,大部分生产商销售数量规模仍较小,2021年全球年销售量超过100台的生产商仅为39家,占比约15%,我国工业级增材制造设备龙头企业铂力特与华曙高科设备销售量分别为140台与133台,且设备业务占比较高,因此企业整体规模与外资相比仍处于起步阶段。
国内主要增材制造设备企业快速发展,先后通过募投实现产能扩张。2019-2022年,国内主要增材制造企业铂力特与华曙高科营业收入持续提升,CAGR分别达42%、43%,且毛利率基本维持50-60%区间(铂力特受到股权激励影响,2021-2022年股份支付费用分别高达1.7、1.6亿元,对净利润与净利率造成较大影响)。此外,铂力特与华曙高科先后通过上市及定增募集资金并开展扩产项目,预计投资总额达34.4亿元。
3、增材制造进入智能电子设备,苹果荣耀入局有望启动产业增长新引擎
目前,3D打印已经成为航空航天等高端设备制造及修复领域的重要技术手段,逐步成为产品研发设计、创新创意及个性化产品的实现手段以及新药研发、临床诊断与治疗的工具。2021年,航空航天是最大的应用领域,占比达到 16.8%,医疗牙科、汽车、消费电子等也是3D打印的主要应用领域。苹果公司今年下半年发布的 Apple Watch Ultra 智能手表的部分钛金属机械部件有望采用3D打印制造。若苹果高端手表年销售1000万块,可能带来1.2-1.6亿元的3D打印设备需求;此外,荣耀发布的Magic V2 手机的轴盖也采用了3D打印技术,假设年销售1000万台,该部分可能为3D打印设备创造5.5-7.6亿元的设备需求。苹果与荣耀的入局,预计将启动3D打印在消费电子领域的应用动力。